Casting.
Process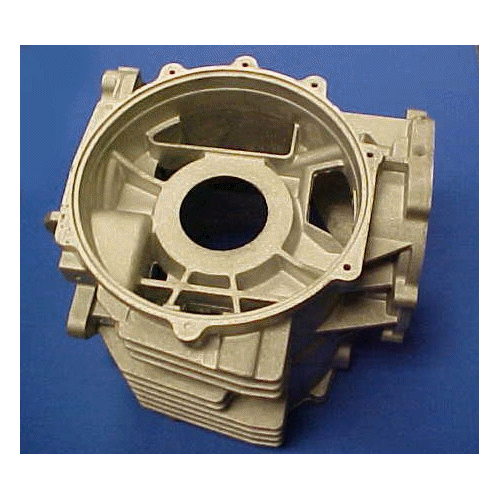
Metal casting is a manufacturing process in which metal is melted and poured into molds where it solidifies into geometrically complex components. Metal casting is unique among metal component forming processes for a variety of reasons.
First, the array of available metal casting processes are capable of producing very simple to extremely complex components in almost any metal, ranging in weight from less than an ounce to several hundred tons. In addition, metal casting processes are available that make it economical to produce a single prototype part, while others achieve their economies in creating multiple units. Understanding the metal casting basics can help you design for manufacturability and utilize processes that meet your specific requirements.
The fundamental process of metal casting consists of five basic
elements:
• Molding—The mold cavity must be formed from a material that will withstand
the operating
temperatures and conditions of the chosen casting process and metal.
• Pouring—The molten metal is poured into the mold and travels through its
passages to fill
the mold cavity.
• Solidification—During the solidification process, the metal cools and
becomes a solid shape.
• Mold Removal—The cooled casting is removed from the mold.
• Secondary Operations—The casting is trimmed, cleaned, heat-treated,
machined, inspected,
painted, etc.
Molding processes can be broken into four general categories: sand casting processes; permanent mold processes; ceramic processes; and rapid prototyping.
Die cast and Permanent Mold Processes: At least three families of molding and casting processes can be categorized as permanent mold processes. These include die casting (high-pressure die casting), low-pressure permanent mold casting and permanent mold casting. Unlike sand casting processes, in which a mold is destroyed after pouring to remove the casting, permanent mold casting uses the mold repeatedly.