Powdered Metal and Metal Injection Molding.
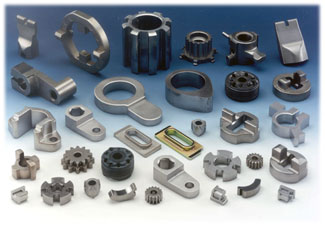
Process
Powder metallurgy, or PM, is a process for forming metal parts by heating compacted metal powders to just below their melting points. Although the process has existed for more than 100 years, over the past quarter century it has become widely recognized as a superior way of producing high-quality parts. PM comprises two different technologies for fabricating semi-dense and fully dense components. The conventional PM process, referred to as press-and-sinter, the other is referred to as the metal injection molding (MIM) process.
Press and Sinter Process: In this process, custom-blended metal powders are fed into a die, compacted into the desired shape, ejected from the die, and then sintered (solid-state diffused) at a temperature below the melting point of the base material in a controlled atmosphere furnace. The compaction step requires the part to be removable from the die in the vertical direction with no cross movements of the tool members. The sintering step creates metallurgical bonds between the powder particles, imparting the necessary mechanical and physical properties to the part.
Conventional PM offers many advantages over the other consolidation methods. It offers the lowest manufacturing cost, including modest tooling costs. It also produces the closest tolerances in the finished parts. Since it is a net-shape processing technology, it yields parts requiring little or no secondary machining operations. Lastly, it makes available to designers and fabricators a wide variety of material systems from which to choose.
Metal Injection Molding Process: offers a manufacturing capability for
producing complex shapes in large quantities. The process utilizes fine metal
powders (typically less than 20 micrometers) which are custom formulated with a
binder (various thermoplastics, waxes, and other materials) into a feedstock which
is granulated and then fed into multiple cavities of a conventional injection
molding machine. After the “green” component is removed, most of the binder is
extracted by thermal or solvent processing and the rest is removed as the
component is sintered (solid-state diffused) in a controlled atmosphere furnace.
The MIM process is very similar to plastic injection molding and high-pressure
die casting, and it can produce much the same shapes and configuration features.
However, it is limited to relatively small, highly complex parts that otherwise
would require extensive finish machining or assembly operations if made by any
other metal forming process.
The advantages of the metal injection molding process lie in its capability to produce mechanical properties nearly equivalent to wrought materials, while being a net-shape process technology with good dimensional tolerance control. Metal injection molded parts offer a nearly unlimited shape and geometric-feature capability, with high production rates through the use of multi-cavity tooling.